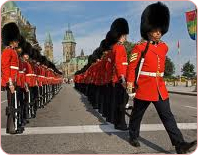
Jack's Lump
Experienced maintenance supervisors and retired, or about to retire, mechanics, fitters, machinists and electricians who served an apprenticeship in the old days know the meaning of Jack's lump.
Times have changed. Training colleges with emphasis on classroom instruction have taken precedence over indentured apprenticeships. Machine tools are complex devices, accurate, efficient and productive. Computer technology and solid state measuring devices have replaced calipers, screwdrivers and the journeyman's eye for the analysis of maintenance problems.
Training methods have changed, too. Jack's lump is a relic of a past age. Maintenance personnel must use sophisticated electronic analyzers to keep operating plant operating efficiently. They no longer scrape and seat plain bearings, they replace them with spares. The same with pumps, valves and other defective equipment. This imposes stringent requirements on instructors and trainers, for maintenance staff must know for certain which device in a system is faulty and needs replacing.
This was a block of steel machine-cut from a bar coated with a thick crust of oily, brittle scale formed during the bar's journey through the rolling mill. With hammer and cold chisel, the apprentice chipped away the hard skin, then spent countless hours over several weeks filing Jack's lump into a gleaming, bright block of shiny steel.
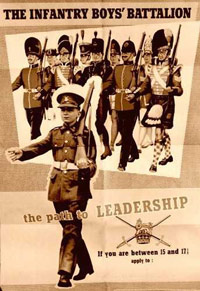
When finished and approved by the journeyman foreman who used calipers, a machinist's square and flatplate to check the work, the apprentice used a ratchet hand drill to bore a three-quarter inch hole in the steel block. (Ratchet hand drills are museum pieces today.) He - there were no she's then - used files to turn the round hole into a square one that again had to pass the foreman's eagle eye for accuracy of squareness.
A block of brass cut and filed was fashioned to fit snugly into the hole. This was the master's way of teaching the apprentice - and sometimes a number of apprentices - to discover the feel of hard steel and soft brass to learn the rudiments of the trade.
In the steam age, before numerically-controlled lathes, shapers, grinders, boring mills and the like came into use, Jack's lump was a necessary part of every apprentice's life: fitter, machinist, mechanic or electrician.
The naval shipyards of Halifax (Nova Scotia) and Portsmouth, the British and Canadian armies, and large manufacturing firms all had thriving training programs for apprentice tradesmen. From these programs flowed a steady stream of qualified journeymen and, for a short time, journeywomen, to join the work force.
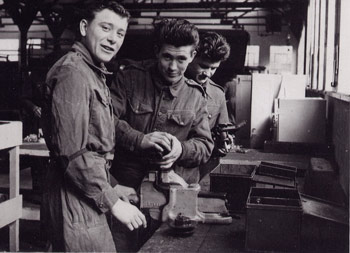
Teaching Fundamentals: The trainer's job is to teach those who maintain and service equipment the essentials of maintenance technology and not to confuse what is important with what is peripheral or non-essential to the job. An electrician does not need to know the effect of the third harmonic on a salient pole generator; a mechanic does not need to know the chemical composition of SA316 stainless steel; a machinist does not need to know the theory of ultrasonic testing for subsurface anomalies.
Trainers frequently confuse what is interesting and academic with what maintenance workers must know. There is a big difference between the two. It is frequently the case that instruction is so broad and ranging that it is difficult for the maintainer to sort the wheat from the chaff.
The important element of any training program is a definition its purpose. How does the maintainer recognize a problem, analyze it, restore a device or a component or a piece of equipment to first-class working order? Definition of purpose, also called the aim or objective, is not easy; yet it is the foundation on which a first-rate training program depends. Define this and the rest follows with relative ease.
Achieving the purpose: The means of achieving the aim of the training is the next essential element. What kind of training will accomplish this goal? What theory must be taught? What aids are required? How much practical instruction should be given? How should maintainers be taught to work safely? How should the message be communicated?
Having chosen the means. the trainer must decide how to prove - that is, how to verify - that the journeyman trainee has understood and will retain the instruction. Is a multiple-choice question paper the answer? Or is an absolute response to questions. without spoon-feeding necessary? In matters of practical training, what proof of knowledge and ability is acceptable?
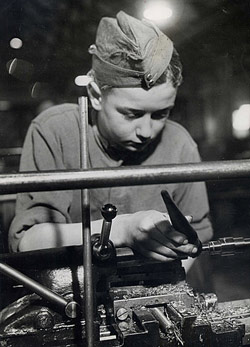
1n a hydro-generating project in Labrador having two 230KV, 180Km-long transmission lines, the owners failed to attract a single experienced mechanic, lineman, electrician or station operator to operate and maintain the system. With ample time before start-up, however, a determined station management hired and trained local people, men and women, to operate and maintain the system. During its first two years in operation, the station had neither a shutdown or equipment failure to jeopardize operation that could not be fixed. Nor did one employee leave to seek greener pastures.
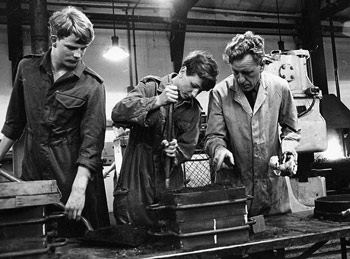
Essential Components: Any successful training program for maintenance personnel has three essential elements, which are:
- A definition of purpose or aim, by course, session, or module;
- A clear course of training and the means of delivery; and
- An equally clear proof that the training is absorbed and understood.
Many large contemporary enterprises assign a good part of their operating budgets to training. Some operate training centres and spend a high proportion of their operating budgets on training programs. Maintenance training has become big business. It never was anything else in well-managed and profitable operations.
Only in the loosest sense can training technology be called scientific, but it must be professional in design and delivery. Logic is as much a part of a good program as of, for example, solid state circuitry. Experts in course development are needed to train the trainers. In maintenance operations, theory is not enough. To succeed, maintenance training requires more than an academic approach. That 'more' is the expertise of the trainer. Without it, training is superficial, ineffective and a waste of time.
An earlier version published as a Special Report in Industrial Maintenance Repair and Overhaul News, November 1990.
The photographs used in this article were provided courtesy Mr. Bob Driscole, an apprentice soldier of the 1950s at Arborfield.
Education Index